Agrandir l’usine de Bhuj et doubler le chiffre d’affaires en seulement 3 ans ?
TNC le 27/02/2023 à 09:13
Grâce à l’agrandissement de son usine installée à Bhuj en Inde, BKT annonce son objectif de croissance : 2 milliards de dollars US de chiffre d'affaires d'ici 2026 et 600 000 t de production annuelle. Un demi milliard de dollars va être investi pour accroître la capacité du site installé non loin du Pakistan. Main-d'œuvre, logements, équipements... le projet voit large en matière d'élargissement communautaire.
BKT vient de dévoiler son projet d’agrandissement de son usine indienne installée à Bhuj dans le nord-ouest du pays, site inauguré en 2015. La feuille de route a été dévoilée et autant dire que l’objectif est ambitieux avec un chiffre d’affaires multiplié par deux d’ici 2026. Le projet de croissance semble plutôt bien ficelé, puisqu’à terme, la production annuelle de pneumatiques devrait atteindre 600 000 tonnes.
Après avoir inauguré le site en 2015, la réputation du manufacturier indien ne semble plus à faire. Conformément à ses ambitions pour les trois prochaines années, la marque devrait poursuivre son chemin selon une logique prévisionniste et d’engagement, tout en restant particulièrement à l’écoute du marché, mais également à force d’audace et de détermination indéfectible.
Usine de Bhuj 2012-2023 : + 262,6 % de surface
À la commercialisation du premier pneu sorti de la chaîne de production du site en 2012, l’usine couvrait 123 ha. À l’époque, l’investissement était de 500 millions de dollars. Soulignons qu’au démarrage des travaux, le paysage était désertique et complétement aride. Il n’y avait ni eau ni électricité. Plusieurs kilomètres de conduites d’eau potable et de lignes électriques ont été posés, permettant aux installations de se développer : 126 ha en 2016, 131 en 2019, 137 en 2021, 258 en 2022. Désormais, fin 2023, il devrait atteindre une surface totale de 323 ha, dont 283 déjà acquis.
Davantage d’espace sous-entend plus de possibilités d’installer des machines et de créer des zones dédiées aux essais. Sans oublier d’accroître les volumes produits. Question croissance, l’indien ne se dégonfle pas. Son activité a progressé de 49 % par rapport à la période antérieure à la pandémie de Covid-19. Bien loin du niveau de production de 2015 (92 t/j), l’usine de Bhuj a bouclé 2022 en dégageant son meilleur résultat, soit 436 t/j.
Du carbone noir auto-produit
L’autre décision stratégique prise par BKT, en vue d’améliorer les performances du site de Bhuj, a été d’investir dans sa propre unité de production de carbone noir. Le site a été mis en service en 2017 et a permis de produire 65 000 t de carbone noir de qualité dure. C’est la matière utilisée pour fabriquer la bande de roulement du pneu. L’année suivante, la production a progressée pour atteindre les 110 000 t, sans oublier l’ajout de la production de carbone doux, utilisé lui pour améliorer la résistance et la durabilité de la gomme. En 2021, la production totale a atteint 138 000 t par an, et en 2022, 165 600 t.
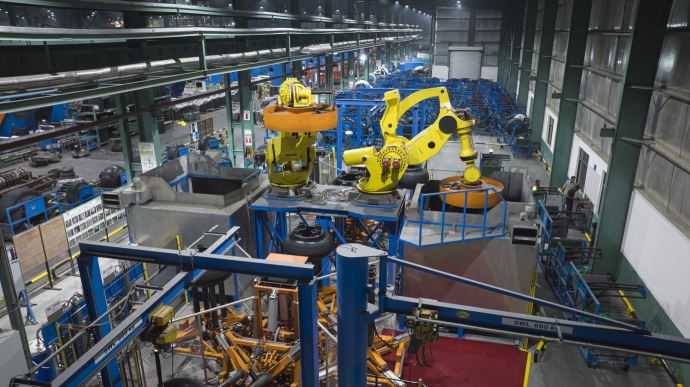
L’objectif pour 2023 est fixé à 198 600 Mt. En outre, le département Recherche et Développement entend intégrer un troisième type de noir de carbone, le « Specialty carbon black ». Il s’agit d’un type de noir de carbone aux propriétés hors norme par rapport à celui utilisé dans les composés de caoutchouc, notamment une haute résistance à la coloration, un niveau élevé de pureté, un niveau réduit de cendres et un très faible niveau de HAP. Il est donc utilisable dans les peintures, plastiques et encres, entre autres.
La famille BKT s’agrandit également
Agrandir l’usine nécessite davantage de capacités de production mais aussi de logistique opérationnelle. L’industriel a donc dû embaucher du personnel spécialisé et s’est adapté en termes de flexibilité au niveau des flux de production et de stockage. Les conditions de sécurité du personnel n’ont pas été mises de côté, elles sont une réelle problématique pour BKT. Fin décembre 2022, les installations faisaient appel à 4 776 employés.
La zone résidentielle, où sont logées les familles du personnel, compte actuellement près de 1 000 personnes. Des services de santé et de scolarisation sont également proposés. C’est une usine à dimension communautaire, constituant un modèle pionnier à l’échelle planétaire dans ce secteur manufacturier. Sans oublier le respect de l’environnement, condition essentielle devant être intégrée aux stratégies de développement de n’importe quelle entreprise dite responsable.
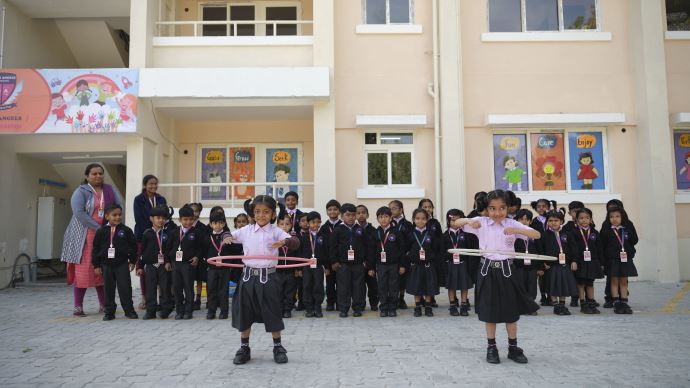
En 2013, la centrale électrique interne avait été installée en vue de produire l’électricité nécessaire au fonctionnement du site. Aujourd’hui, les panneaux solaires et l’unité de cogénération assurent l’autoproduction. En 2022, la centrale de cogénération avait été agrandie, passant de 20 MW à 40 MW. Des projets sont toujours à l’étude pour accroître la puissance des ressources renouvelables autoproduites. Autre priorité : l’eau. Elle est au cœur de la voie vertueuse de BKT vers la durabilité. Depuis 2019, le principe Zero Liquid Discharge (ZLD) a été adopté, signifiant qu’aucun déchet liquide n’est rejeté à l’extérieur de l’usine. Toute l’eau utilisée est traitée, purifiée, puis réutilisée. Le principe ZLD est simple : conserver les ressources en eau, réduire l’impact environnemental des rejets d’eaux usées et améliorer l’efficacité globale ainsi que la durabilité de l’usine.
Diminuer la consommation énergétique de 70 %
Retour sur la question du carbone. La matière est acheminée de l’usine de production vers l’unité de fabrication des pneus, via des silos mobiles transportés pneumatiquement vers la zone de stockage. Résultat : des économies devraient être réalisées en matière de conditionnement, soit 100 000 conteneurs à terme.
À souligner aussi, la réduction de la consommation d’énergie. Chaque système de transfert est contrôlé en fonction du poids et de l’énergie utilisée. L’objectif étant de diminuer la consommation d’énergie de 70 %. Exprimé en kg de CO2 émis chaque année, cela représente plus de 2 millions, soit les émissions de 5 000 appartements de 100 m². En parallèle, le gaz utilisé pour fabriquer le carbone noir se retrouve désormais dans une usine de cogénération, à même de réutiliser 75 000 m3 de gaz par an. Ce qui revient à économiser 215 000 t de charbon chaque année.