50 000 € d’investissement pour autoconstruire un séchoir en grange de luzerne
TNC le 15/03/2019 à 05:57
C’est à La Comté (62) que Benoît Hannebique, associé avec ses deux parents, élève un troupeau de 70 vaches laitières. En 2013, père et fils se lancent dans la construction d'un séchoir en grange. Leur objectif : sécher de la luzerne afin d'améliorer l'autonomie protéique de l'exploitation. Après plusieurs années d'expérience, aucun regret pour le jeune éleveur même si certains doutes planent encore sur la rentabilité du séchoir au vu du temps passé.
Gagner en autonomie protéique : voilà le but de beaucoup d’élevages. Les associés du Gaec Hannebique, situé à La Comté (Pas de Calais) ont atteint leurs objectifs en implantant de la luzerne mais aussi en installant un séchoir en grange. « La luzerne nous permettait de diversifier notre assolement car nous avions des problèmes de vulpin résistant », témoigne Benoît Hannebique. Sur la ferme, elle est alors semée derrière un escourgeon et est suivie d’un blé.
Sécher la luzerne à plat et la stocker dans une autre case
Associé avec ses parents depuis 2016, Benoît cultive 150 ha et élève 70 vaches laitières prim’holsteins et leur suite. Depuis 2013, les exploitants cultivent et sèchent la luzerne à la ferme grâce au séchoir qu’ils ont entièrement autoconstruit. « On fait actuellement 4 coupes/an sur nos 10 ha de luzerne. Les parcelles sont en place pour trois ans. On a commencé il y a quelques années avec une plus grosse surface et on vendait une partie de notre production mais la vente nous a vite pris trop de temps. On avait aussi fortement réduit le maïs ensilage au profit du maïs grain humide couplé à la luzerne mais le gel a pénalisé la dernière récolte donc on a fait machine arrière en réintégrant du maïs plante entière. En revanche, on prévoit pour l’an prochain de l’ensiler en coupe haute afin de le densifier en UF. »
Pour en revenir à la luzerne, celle-ci est récoltée à l’aide d’une faucheuse conditionneuse. L’andain est ramassé deux à trois jours après la coupe. Il n’y a aucun fanage au champ pour limiter l’effeuillage. La luzerne est ensuite déposée dans le séchoir et y reste durant sept jours. « Le séchage se fait à plat, explique le jeune agriculteur. Le tas de fourrage fait en général 2 m de haut. Il peut atteindre les 5 m pour les premières coupes mais c’est le maximum. »
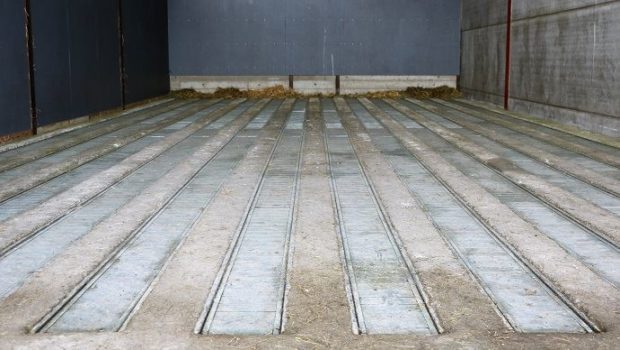
Le séchoir en grange totalement autoconstruit du Gaec Hannebique se présente en deux cases comme celle-ci. (©TNC)
Ce type d’installation nécessite de stocker le fourrage sec ailleurs pour libérer la place. De ce fait, une partie du bâtiment est consacrée au stockage. Les éleveurs ont alors la possibilité de stocker 12 ha, soit 120 t de luzerne au sec. « L’avantage de ce système est que nous y allons au godet : l’achat d’une griffe suspendue n’a pas été nécessaire. Nous pouvons aussi profiter du séchoir pour d’autres cultures. L’année dernière par exemple, nous y avons séché du colza. » Autre avantage, les différentes coupes ne se mélangent pas dans le séchoir.
Un séchoir en grange totalement autoconstruit
Père et fils ont passé de longues soirées et des week-ends complets à monter leur séchoir. Il se divise en deux cases. L’air entre alors dans le bâtiment par le pignon et se réchauffe dans la double toiture composée de panneaux sandwich. Un générateur d’air chaud au fioul de 250 kW a aussi été installé au cas où le réchauffement de l’air naturel serait insuffisant. « La luzerne sèche dès qu’on a un écart de 2 à 3°C avec la température extérieure. Ça peut vite chauffer. On monte à 50°C maximum. En effet, il ne faut pas dépasser les 70°C au risque de faire chuter les valeurs alimentaires du fourrage (en moyenne à 21,5 de MAT). »
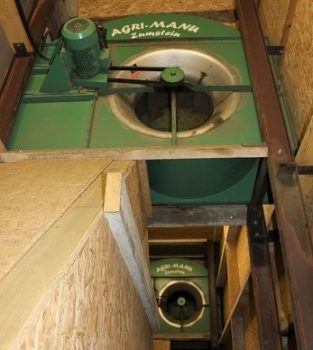
Deux ventilateurs (un pour chaque case) renvoient l’air de la toiture vers le dessous du fourrage. (©TNC)
Un variateur de fréquence a été installé sur les ventilateurs pour diminuer la consommation d’énergie en modulant la puissance du séchage. Ainsi, la sonde hygrométrique fait varier la vitesse des ventilateurs.
Les associés ont préféré se tourner vers un générateur d’air chaud plutôt qu’un déshumidificateur car il leur permet de continuer à sécher le fourrage par temps humide et ainsi éviter que ça fermente. De plus, cela leur coûtait moins cher à l’achat. Aujourd’hui, avec l’expérience, les éleveurs se demandent si le déshumidificateur n’aurait pas permis de réduire leur consommation d’électricité.
Pour ceux qui souhaiteraient se lancer, Benoît recommande : « Le mieux est de sécher le fourrage en quatre jours afin d’éviter l’apparition de mycotoxines. Nous le faisons en sept jours et les analyses nous prouvent que ça n’est pas assez rapide. Heureusement, nous distribuons une ration complète donc les mycotoxines de la luzerne se retrouvent diluées. » Autre préconisation : « Dans un tel système, il faut compter 4 m2 de toiture pour 1 m2 de séchoir. »
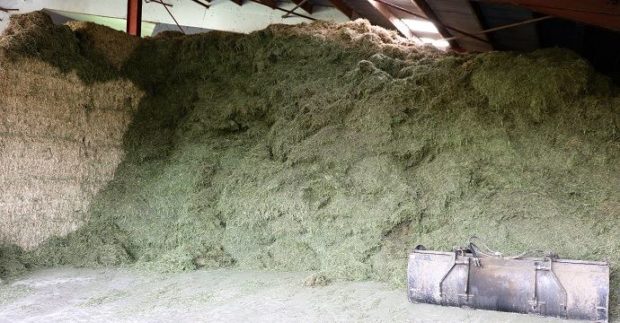
Une partie du bâtiment est consacrée au stockage de luzerne séchée. Cette case peut accueillir jusqu’à 120 tonnes de fourrage, soit 12 ha. (©TNC)
Une rentabilité qui reste à calculer
Fait maison, le séchoir a coûté au Gaec 50 000 € hors coût de main d’œuvre. Les éleveurs estiment que son prix aurait été multiplié par trois en comptant la main d’œuvre. De plus, ils ont bénéficié d’aides comme le PMBE (plan de modernisation des bâtiments agricoles) et le PPE (plan de performance énergétique) qui ont financé près de 40 % du séchoir. À cela s’ajoute le prix du bâtiment qui sert aussi de stockage pour la paille et la luzerne sèche.
Les éleveurs ont fait le choix de ne pas prendre de griffe suspendue et leur système leur permet de vider facilement au télescopique. « C’est une véritable économie. Pour une griffe, il fallait rajouter pas loin de 100 000 € et on n’en avait pas l’utilité. Elle sert vraiment aux éleveurs de montagne qui distribuent directement à l’auge avec. Par chez nous, ça n’est pas rentable si c’est pour remettre le fourrage dans une mélangeuse derrière. »
Benoît témoigne : « Grâce à la luzerne, nous faisons aujourd’hui 35 à 40 % d’économie sur l’achat des concentrés. On travaillait auparavant en soja/colza à hauteur de 5,5 kg/VL/j. Aujourd’hui, nous ne travaillons qu’en colza (3,5 kg/VL/j) car nous sommes passés en filière pâturage et non OGM. Même si l’économie est difficile à chiffrer avec ces changements, elle apparaît réellement dans nos résultats. »
« Le séchoir nous permet de distribuer de la luzerne à tout le monde toute l’année. Seules les vaches taries n’en ont pas. On supprime le tourteau aux génisses l’hiver et les petits veaux ont de la luzerne à volonté dès leur plus jeune âge. C’est un produit coûteux mais on observe de réels bénéfices chez les animaux : la ration est bien plus fibreuse qu’avant, les animaux ruminent davantage, les frais vétos ont diminué, on a réduit le concentré et on ne distribue plus d’hépato, de propylène ou de bicarbonate. On est en quelque sorte autonomes puisqu’on produit du colza sur l’exploitation. Même si ce n’est pas nous qui le transformons en tourteau, cela reste local et c’est important pour nous. »
Du côté de l’investissement dans le séchoir, les associés n’ont pas de regret mais ils se posent tout de même des questions quant à sa rentabilité : « Nous avons quand même passé un certain temps à le construire et c’est beaucoup de manutention en pleine saison. On compte 3 h de travail/coupe/ha (2 ha/h pour la fauche, 1 ha/h pour le ramassage, 1 ha/h de manutention à 2 à la récolte et 30 min/ha pour tout ressortir du séchoir). Tout ceci multiplié par 4 coupes/an, ça fait quand même 12 h/ha/an ! » Benoît plaisante : « Finalement, plus le concentré est cher et plus le séchoir sera rentable. Attention cependant, il ne faut pas qu’il grimpe trop haut car on utilise toujours du tourteau ! »
Si c’était à refaire, Benoît et son père expliquent : « On ne ferait plus qu’une seule grande case, on isolerait le béton car on perd beaucoup de chaleur par le sol et on ferait une toiture plus petite avec pourquoi pas des panneaux solaires. »